1.Integral cutting edges
remove the burr from the front of the hole as
the tool enters the hole.
2.The slotted design allows the tool to
'collapse' under load as the tool feeds through
the workpiece. The crowned and polished top
surface of the cutting edges will not mar the
inside surface of the hole.
3.The back of the hole is deburred on the retun
stroke.
|
Feed-In---Feed-Thru-----Feed-out---Finished-up |
|
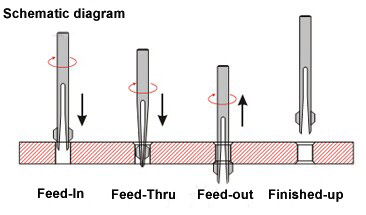 |
Design features:
1.The
Burr-off tool is suited to mass-production operation and readily adaptable to all types of procuction machines,
2.used by the leading automobile markesall over the world. |
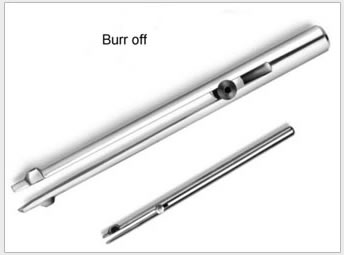 |
Standard tool
specifications
1. Single cutting
edge

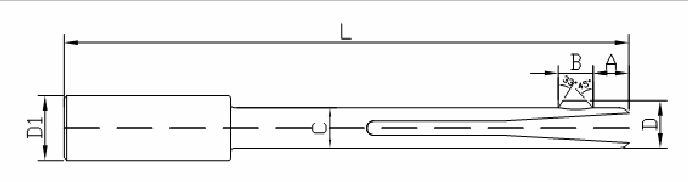
Tolerance of shank
diameter from BO-0.8---BO-6: +0,-0.05
Special sizes and
Titanium Nitride coated tools are available on request.
BO-0.8-B0-6: Fix
shank
CODE |
Drilled Hole |
Arbor(D1) |
C |
OAL(L) |
Dim.A |
Dim.B |
Dim.D |
R.P.M |
BO-0.8 |
0.8-0.9 |
3 |
0.7 |
45 |
1 |
1.5 |
1.05 |
1800 |
BO-0.9 |
0.9-1.0 |
3 |
0.8 |
45 |
1 |
1.5 |
1.2 |
1800 |
BO-1.0 |
1.0-1.1 |
3 |
0.9 |
45 |
1 |
1.5 |
1.35 |
1800 |
BO-1.1 |
1.1-1.2 |
3 |
1 |
45 |
1 |
1.5 |
1.5 |
1800 |
BO-1.2 |
1.2-1.3 |
3 |
1.1 |
45 |
1 |
1.5 |
1.65 |
1800 |
BO-1.3 |
1.3-1.4 |
3 |
1.2 |
45 |
1 |
1.5 |
1.8 |
1800 |
BO-1.4 |
1.4-1.5 |
3 |
1.3 |
45 |
1 |
1.5 |
1.95 |
1800 |
*BO-1.5# |
1.5-1.6 |
3 |
1.4 |
50 |
2 |
2.5 |
2.1 |
1500 |
*BO-1.6# |
1.6-1.7 |
3 |
1.5 |
50 |
2 |
2.5 |
2.25 |
1500 |
*BO-1.7# |
1.7-1.8 |
3 |
1.6 |
50 |
2 |
2.5 |
2.4 |
1500 |
*BO-1.8# |
1.8-1.9 |
3 |
1.7 |
60 |
2 |
2.5 |
2.55 |
1500 |
*BO-1.9# |
1.9-2.0 |
3 |
1.8 |
60 |
2 |
2.5 |
2.65 |
1500 |
*BO-2# |
2.0-2.2 |
3 |
1.9 |
60 |
2 |
2.5 |
2.8 |
1500 |
*BO-4# |
2.2-2.4 |
3 |
2.1 |
80 |
2 |
2.5 |
3.15 |
1500 |
*BO-5# |
2.4-2.6 |
3 |
2.3 |
80 |
2 |
2.5 |
3.45 |
1500 |
Notice: No BO-6, BO-5 can be used for processing for 2.7mm hole.
2. Single cutting
edge
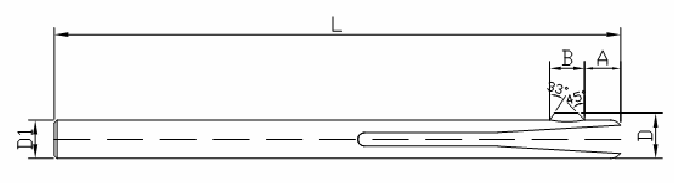
Tolerance of shank
diameter from BO-7---BO13: +0,-0.03
Special sizes and
Tianium Nitride coated tools are available on request.
CODE |
Drilled Hole |
D1 |
OAL(L) |
Dim.A |
Dim.B |
Dim.D |
R.P.M |
*BO-7 |
2.8-3.18 |
2.75 |
101.6 |
3.18 |
4.45 |
4 |
1200 |
*BO-8 |
3.18-3.55 |
3.15 |
101.6 |
3.18 |
4.45 |
4.34 |
1200 |
*BO-9 |
3.55-3.96 |
3.58 |
101.6 |
3.18 |
4.45 |
4.75 |
1200 |
*BO-10 |
3.96-4.36 |
3.9 |
101.6 |
3.18 |
4.45 |
5.54 |
1200 |
*BO-11 |
4.36-4.74 |
4.34 |
101.6 |
3.18 |
4.45 |
5.94 |
1200 |
*BO-12 |
4.74-5.15 |
4.72 |
101.6 |
3.18 |
6.22 |
6.35 |
1200 |
*BO-13 |
5.15-5.56 |
5.13 |
101.6 |
3.18 |
6.22 |
6.78 |
1200 |
3.Double cutting
edge
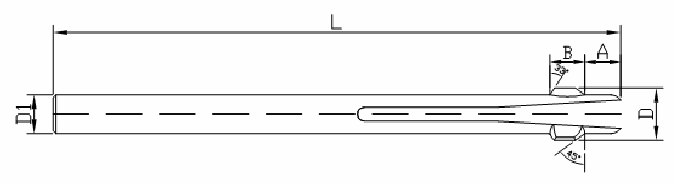
Tolerance of arbor
diameter from BO-14---BO50: +0,-0.05
Special sizes and
Titanium Nitride coated tools are available on request.
CODE |
Drilled Hole |
D1 |
OAL(L) |
Dim.A |
Dim.B |
Dim.D |
R.P.M |
BO-14 |
5.56-5.94 |
5.54 |
101.6 |
6.48 |
6.22 |
7.92 |
800-1000 |
BO-15 |
5.94-6.35 |
5.92 |
101.6 |
6.48 |
6.22 |
8.33 |
800-1000 |
BO-16 |
6.35-6.75 |
6.32 |
101.6 |
6.48 |
6.22 |
8.71 |
800-1000 |
BO-17 |
6.75-7.13 |
6.73 |
101.6 |
6.48 |
6.22 |
9.12 |
800-1000 |
BO-18 |
7.13-7.54 |
7.11 |
101.6 |
6.48 |
6.22 |
9.53 |
800-1000 |
BO-19 |
7.54-7.95 |
7.52 |
101.6 |
7.24 |
6.48 |
9.91 |
800-1000 |
BO-20 |
7.95-8.33 |
7.92 |
101.6 |
7.24 |
6.48 |
10.31 |
800-1000 |
BO-21 |
8.33-8.71 |
8.31 |
101.6 |
7.24 |
6.48 |
10.72 |
800-1000 |
BO-22 |
8.71-9.11 |
8.69 |
101.6 |
7.24 |
6.48 |
11.1 |
800-1000 |
4. Changeable cutting edge
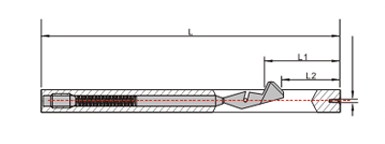
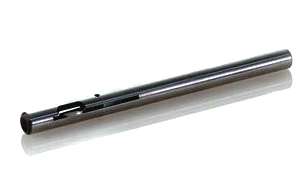
|
CODE |
Drilled Hole |
L |
L1 |
Cut Code |
R.P.M |
|
BO-23 |
10 |
163.5 |
25.4 |
2# |
800-1000 |
|
BO-24 |
11 |
163.5 |
26.1 |
2.5# |
800-1000 |
|
BO-25 |
12 |
163.5 |
27.1 |
2.5# |
600 |
|
BO-26 |
13 |
163.5 |
28.1 |
2.5# |
600 |
|
BO-27 |
14 |
163.5 |
33.2 |
3# |
600 |
|
BO-28 |
15 |
163.5 |
34.2 |
2.5# |
600 |
|
BO-29 |
16 |
163.5 |
35.2 |
2.5# |
600 |
|
BO-30 |
17 |
163.5 |
36.2 |
2.5# |
600 |
|
BO-31 |
18 |
163.5 |
37.2 |
2.5# |
600 |
|
BO-32 |
19 |
163.5 |
38.2 |
2.5# |
600 |
|
BO-33 |
20 |
171.4 |
39.1 |
2.5# |
600 |
|
BO-34 |
21 |
171.4 |
|
2.5# |
600 |
|
BO-35 |
22 |
171.4 |
|
2.5# |
600 |
|
BO-36 |
23 |
171.4 |
|
2.5# |
600 |
|
BO-37 |
24 |
171.4 |
|
2.5# |
600 |
|
BO-38 |
25 |
171.4 |
|
2.5# |
600 |
Tool adjustment and operating recommendations
Fast and easy adjustment
The amount of edge break will vary with the hardness of
the
material.Loosen the screw on the sliding
tension-adjustment
mechanism and move it up or down the length of the slot
for
more or less stock removal.
Speed and feeds
As with burr off,use the same speed and fee rate as you
would
run a standard HSS drill.
Tool maintenance and edge resharpening
Regrinding Guidelines:To extend the life of the tool,the
cutting edges maybe regrinded up to four times.
Inspect for grit and foreign matter during and after
each operation.Clean as needed.
The burr off should be inspected periodically for grit
and foreign
particles,and cleaned as necessary.
The cutting edges may be reground up to four times in
order to
extend tool life.Refer to Figure 2 below for proper
regrind procedure. |
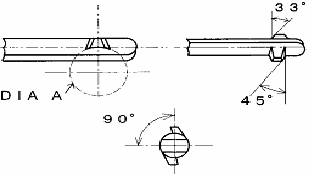 |
Grinding wheel Dia.A |
15.7 |
19.1 |
22.1 |
31.7 |
|
Hand grind
face.0.25mm-0.38mm.
preferably
with an abrasice wheel with the diameter
shown in the
chart(''A''diameter).Flat face grind is optional